2025년 산업용 레이저 머신이 운영 비용을 줄이는 5가지 방법
정밀 절단으로 자재 낭비 제거
산업용 응용에서 마이크론 수준의 정확도
산업용 레이저 기계에서의 마이크론 수준의 정밀도는 항공우주 및 자동차 분야와 같이 정밀도가 가장 중요한 분야에서 매우 중요합니다. 이러한 수준의 정밀도는 부품들이 정확한 사양에 맞춰 제조되어 자재 낭비를 크게 줄일 수 있습니다. 연구에 따르면 레이저 절단 기술은 기존의 전통적인 방법에 비해 자재 폐기물을 최대 25%까지 줄일 수 있어 비용 절감과 자원 관리 개선으로 이어집니다. 특히 티타늄이나 스테인리스강과 같은 고가의 자재를 사용할 때 이러한 효율성은 더욱 유용합니다. 또한, 이러한 기계에 탑재된 고급 센서와 피드백 시스템은 절단 중 실시간 조정이 가능하게 하여 정확도를 한층 더 높이고, 불필요한 스크랩을 최소화함으로써 지속 가능성 목표 달성에 기여합니다.
소프트웨어 기반 중첩 최적화
소프트웨어 기반 중첩 최적화는 재료 사용을 최대화하여 레이저 절단 효율성을 향상시키는 데 중요한 역할을 합니다. 중첩 소프트웨어는 폐기물을 줄이기 위해 부품을 시트 위에 전략적으로 배열하며, 재료와 형상의 복잡성에 따라 재료 수율을 10-30% 개선합니다. 이러한 솔루션은 종종 제작자가 실제 절단을 시작하기 전에 다양한 레이아웃 옵션을 평가할 수 있도록 시뮬레이션을 포함합니다. 이는 최적의 자원 활용을 보장할 뿐만 아니라 비용을 크게 절감하는 데 도움을 줍니다. 소프트웨어에서 제공하는 시뮬레이션은 값비싼 실수를 방지하고 기업이 정보에 근거한 결정을 내릴 수 있게 하여 레이저 절단기를 사용할 때의 수익성을 증대시킵니다.
자동화로 인한 인건비 감소
24/7 CNC 운영 능력
CNC 레이저 머신의 통합을 통해 제조업체는 연속적이고 자동화된 생산을 달성할 수 있습니다. 이 기능은 지속적인 수작업 개입의 필요성을 제거하여 상당한 인건비를 절감합니다. 이 머신들은 24시간 운영됨으로써 생산성을 최대 50%까지 향상시킬 수 있으며, 최소한의 인력으로도 높은 출력을 보장합니다. 이 기술을 도입한 회사들은 운영 시간과 인건비가 눈에 띄게 줄어들었다고 보고하며, 이는 중요한 재정적 이점으로 이어집니다. 프로세스의 자동화는 대규모 수요를 원활하게 충족시키면서도 많은 인력 부담 없이 대응하는 데 도움을 줍니다.
디지털 워크플로우를 통한 오류 감소
CNC 작업 내에서 디지털 워크플로우를 도입하면 수작업 설정과 관련된 오류를 크게 줄일 수 있습니다. 작업 일정 관리, 자재 추적 및 품질 관리를 위한 소프트웨어 시스템을 활용하면 프로세스가 효율화되어 실수를 줄이고 비용이 많이 드는 재작업의 필요성을 감소시킬 수 있습니다. 다양한 제조업체들의 사례에 따르면 이러한 디지털 통합을 통해 재작업 비용을 최대 20%까지 절감할 수 있다고 합니다. 또한 완전한 디지털 워크플로우는 생산 전반의 조율이 잘 이루어지도록 보장하여 전체적인 효율성과 생산성 향상에 기여합니다. 이와 같은 디지털 접근 방식은 제품 품질을 높이는 동시에 운영을 간소화하므로 현대 제조업에서 필수적인 요소로 자리 잡고 있습니다.
에너지 효율적인 운영으로 전력 절약
섬유 레이저 전력 소비율
현대 섬유 레이저는 에너지 효율성이 뛰어나 전통적인 CO2 레이저보다 약 50% 적은 전력을 소비합니다. 이 전력 사용량의 감소는 제조업체들에게 상당한 에너지 비용 절감으로 이어집니다. 섬유 레이저 기술을 운영에 통합하면 기업은 규모와 생산량에 따라 매년 최대 1만 달러를 절약할 수 있습니다. 이는 섬유 레이저를 경제적으로 실현 가능한 선택지로 만들 뿐만 아니라, 전체 에너지 소비와 냉각 비용을 줄여 환경적으로도 유리합니다. 낮은 에너지 요구량이라는 장점 덕분에 섬유 레이저는 산업용 응용 분야에서 지속 가능하고 비용 효율적인 선택지로 자리잡고 있습니다.
냉각 시스템 혁신
혁신적인 냉각 시스템은 레이저 기계의 에너지 효율을 최적화하는 데 중요한 역할을 합니다. 이러한 선진적인 냉각 솔루션은 운영 효율성을 유지하고 장치 수명을 연장하며 에너지 낭비를 줄이는 데 도움을 줍니다. 최신 냉각 기술을 채택함으로써 기업은 열 관리와 관련된 에너지 사용량을 최대 30%까지 절감할 수 있습니다. 일부 제조업체들은 성능을 더욱 향상시키고 지속 가능한 실천에 기여하는 폐쇄형 냉각 시스템을 도입했습니다. 냉각 기술에서 이러한 혁신은 레이저 기계의 운영 효율성을 높일 뿐만 아니라 더 친환경적인 제조 프로세스로의 전환을 강조합니다.
요약하면, 감소된 전력 소비와 선진화된 냉각 기술의 결합된 이점들은 비용을 절감하고 에너지 효율적인 운영을 촉진하려는 제조업체들에게 섬유 레이저 머신이 훌륭한 선택임을 보여줍니다. 산업들이 지속 가능한 솔루션을 계속 추구함에 따라, 이러한 기술들은 환경적 영향을 고려하면서 생산 목표를 달성할 방법을 제공합니다.
저유지 설계로 다운타임 최소화
밀폐형 광학 경로 보호
현대 레이저 기계에서 밀폐된 광학 경로는 먼지와 이물질의 축적을 방지하여 유지보수 필요성을 크게 줄이는 뚜렷한 장점을 제공합니다. 이러한 설계 특징은 청소 및 기타 유지 관리 작업에 필요한 다운타임을 줄여 기계의 운영 효율성을 향상시킵니다. 실제로 밀폐된 광학 경로를 사용하는 기업들은 유지보수 간격이 연장됨에 따라 생산성이 크게 증가한다는 것을 보고하고 있습니다. 이러한 보호 조치를 시행하면 레이저 기계가 최적의 성능을 발휘하면서도 최소한의 개입으로 일관된 성능을 유지하고 정밀 부품의 신뢰성을 보존할 수 있습니다.
부품 수명 비교
비교 연구들은 항상 견고한 부품으로 장착된 레이저가 표준 기계보다 수명이 최대 다섯 배 길어지고, 교체 주기를 줄일 수 있음을 강조해왔다. 고품질 부품에 투자하면 예상치 못한 고장과 서비스 중단을 줄이는 것은 물론, 시간이 지남에 따라 수리 비용에서도 큰 절감 효과를 볼 수 있다. 또한, 고급 부품을 지원하는 보증 및 서비스 계약은 기업에게 장기적인 신뢰성에 대한 안심을 제공하며, 운영이 더 원활하게 진행되고 중단이 적게 발생하도록 한다. 레이저 머신의 내구성을 우선시함으로써 제조업체는 비효율적인 시간을 효과적으로 줄이고 효율성을 높이며 전체 생산성을 최적화할 수 있다.
2025년을 위한 최고의 비용 절감 산업용 레이저 머신
레이저 조각 및 절단 머신 1310: 안정성과 정확성
그 레이저 조각 및 절단 기계 1310 우수한 안정성으로 두각을 나타내며, 정밀한 작업이 필요한 까다로운 환경에서도 뛰어납니다. 이 기계의 고급 기술은 오류를 최소화하여 출력 품질을 크게 향상시키고 재료 낭비를 줄입니다. 많은 사용자들이 생산 효율성이 최대 20% 개선되었음을 보고했으며, 이는 제조 비용에서 상당한 절감으로 이어집니다. 이러한 기계들은 정확성과 생산성을 저하시키지 않고 비용 효율적인 솔루션을 찾는 기업들에게 필수적입니다.
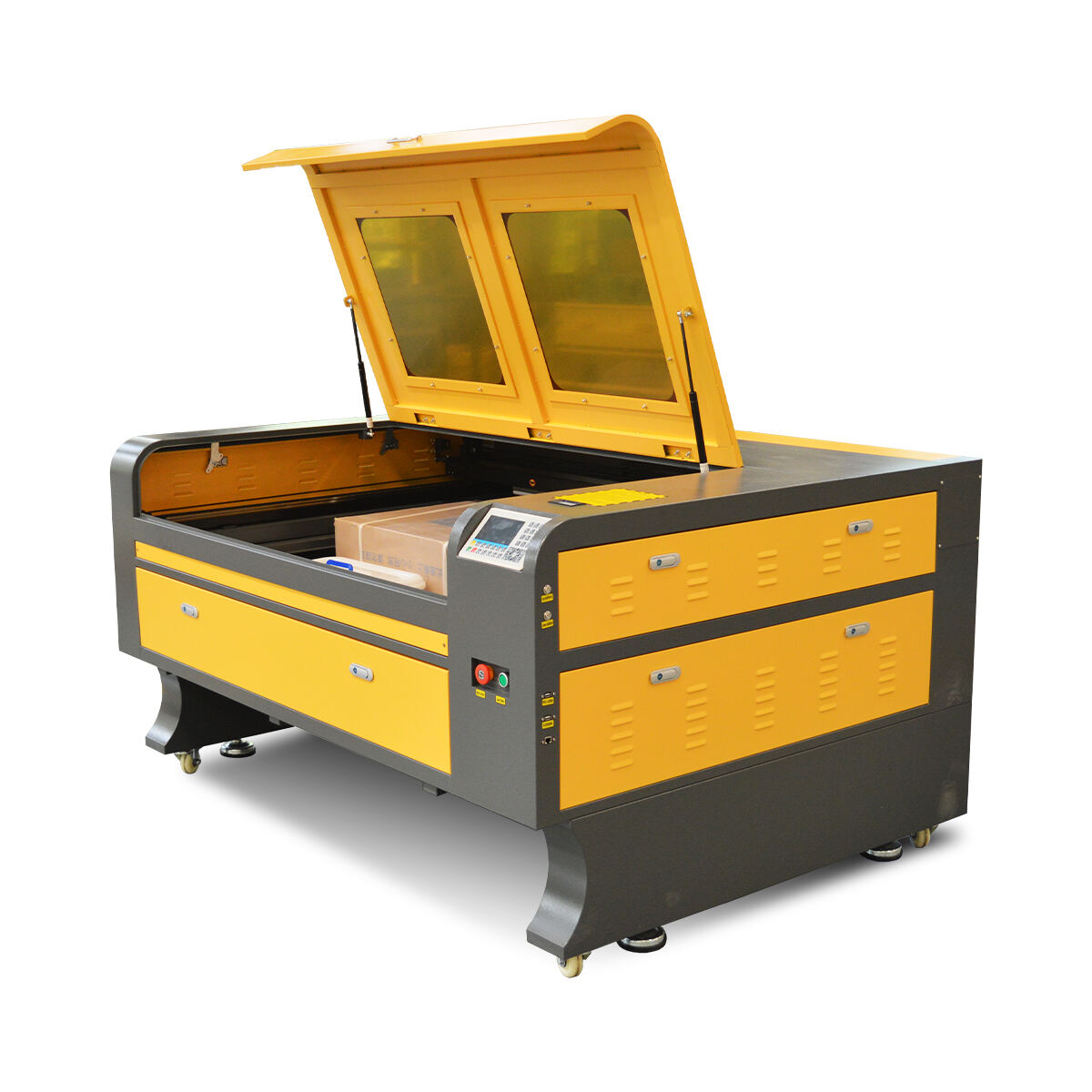
레이저 조각 및 절단기 1390: 확대된 작업 영역
그 레이저 조각 및 절단 기계 1390 작업 영역이 넓어 작업자가 더 큰 프로젝트를 관리하고 여러 작업을 동시에 수행할 수 있다는 점에서 칭찬받고 있습니다. 증가된 작업 공간 덕분에 약 30%의 턴어라운드 시간 개선이 눈에 띄게 나타납니다. 이 개선은 비즈니스 생산성을 극대화하는 데 도움을 주는 동시에 생산 과정을 최적화하여 인건비를 줄이고 순이익을 높입니다.
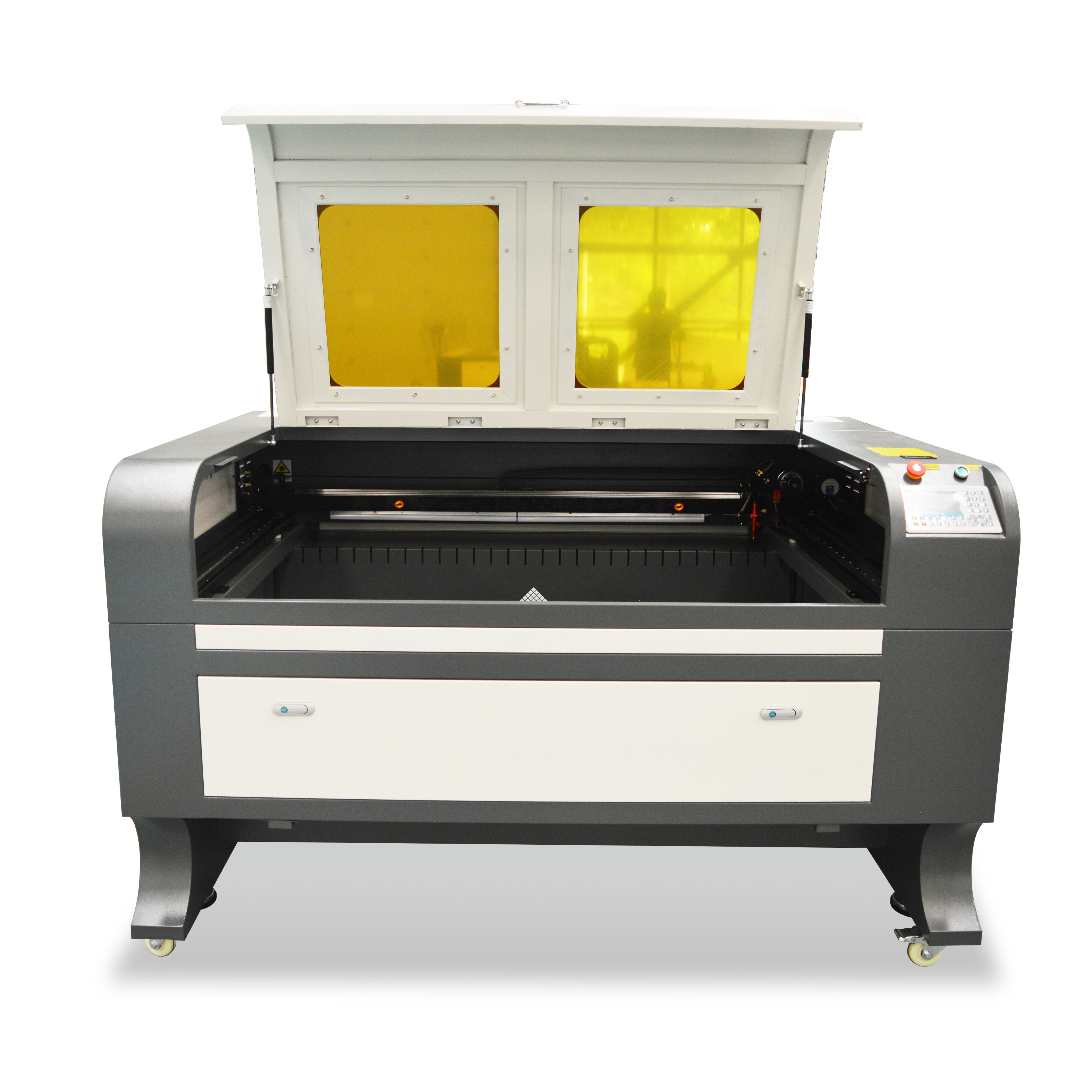
레이저 조각 및 절단 머신 1530: 대형 서식 효율성
대형 서식 프로젝트를 위해 설계된 레이저 조각 및 절단 기계 1530 대규모 주문에 대해 빠른 처리 시간을 제공하여 속도와 다용성이 요구되는 산업 분야에서 큰 자산이 됩니다. 이 기계는 무거운 작업 부하 하에서도 일관된 품질을 유지하는 능력이 다른 모델들과 비교해 우수한 성능을 보여주어 투자 수익률(ROI) 증가로 이어졌습니다. 사용자들은 이 기계의 신뢰성 있는 성능이 고객 만족도를 높이고 엄격한 비즈니스 요구사항을 타협 없이 충족시킨다고 평가합니다.
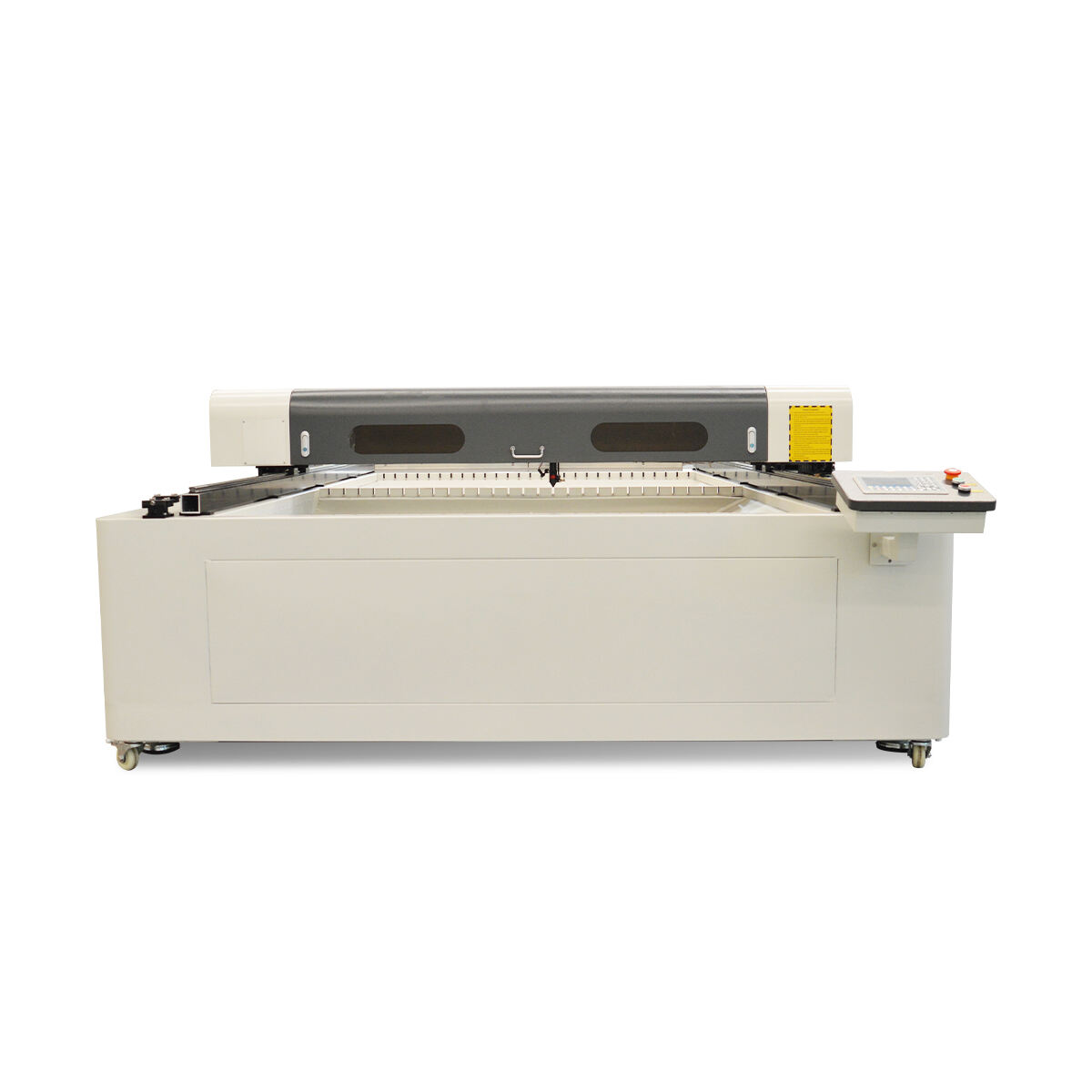
레이저 조각 및 절단 기계 3020: 콤팩트한 산업용 디자인
그 레이저 조각 및 절단 기계 3020 콤팩트한 설계 덕분에 공간이 제한된 시설에 적합하며, 성능 능력에서는 타협이 없습니다. 이 기계는 정밀 절단을 소규모 규모에서 실현하기 위해 고도의 기술을 활용하여 운영 비용을 크게 절감합니다. 생산량을 극대화하면서도 층면적 임대 및 운영 비용을 절약하려는 사용자들 사이에서 선호되는 선택입니다.
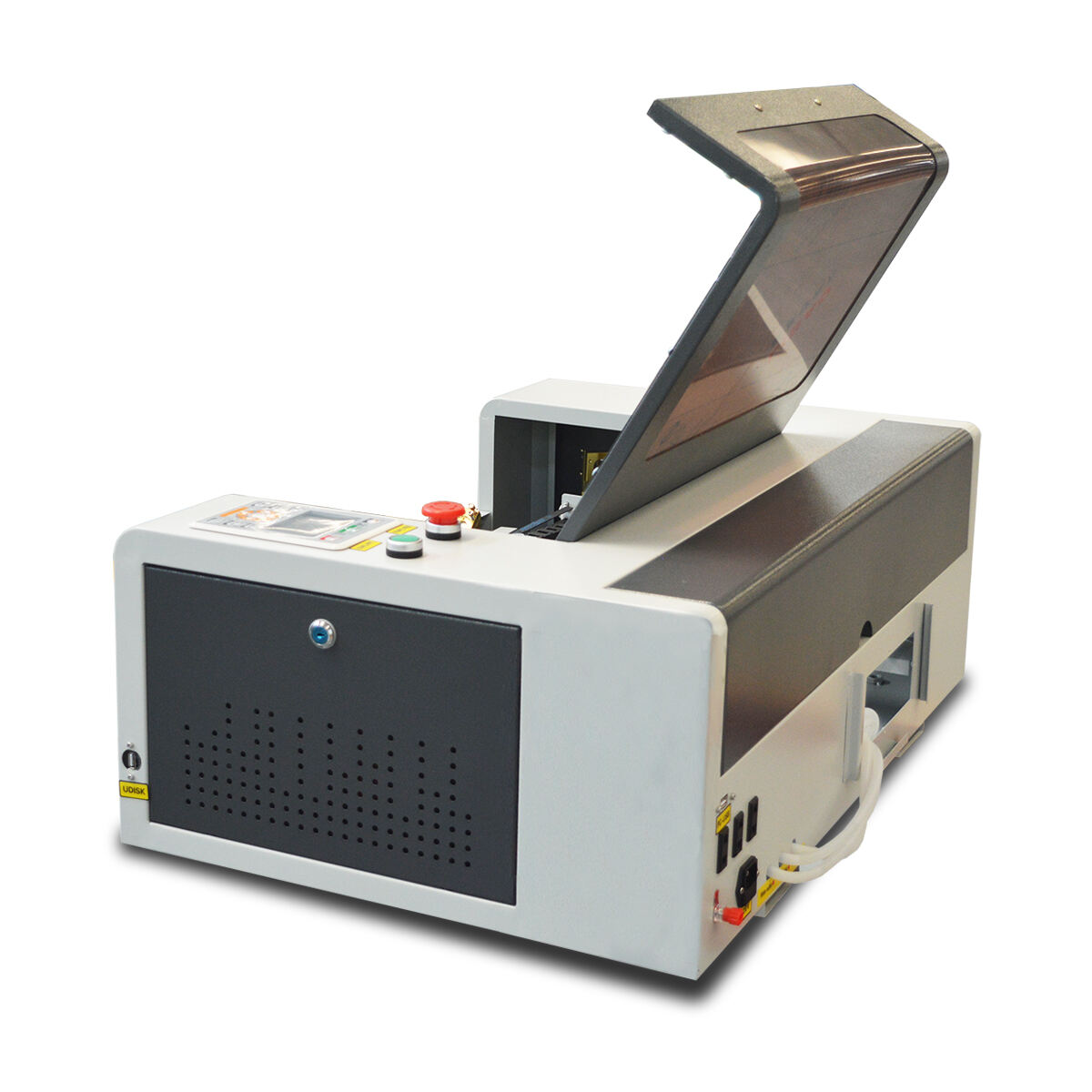
포터블 레이저 마킹 머신: 에너지 효율적인 유연성
포터블 레이저 마킹 머신 유연성과 에너지 효율성을 결합하여 다양한 마킹 솔루션을 필요로 하는 기업들에게 이상적입니다. 이 기계들은 다양한 작업 크기에 적응할 수 있으며, 전통적인 방법에 비해 약 25%의 에너지 소비를 크게 줄입니다. 이동성과 효율성의 조합은 특히 에너지 비용을 최소화하면서 운영 유연성을 유지하려는 중소기업에게 점점 더 매력적으로 다가갑니다.
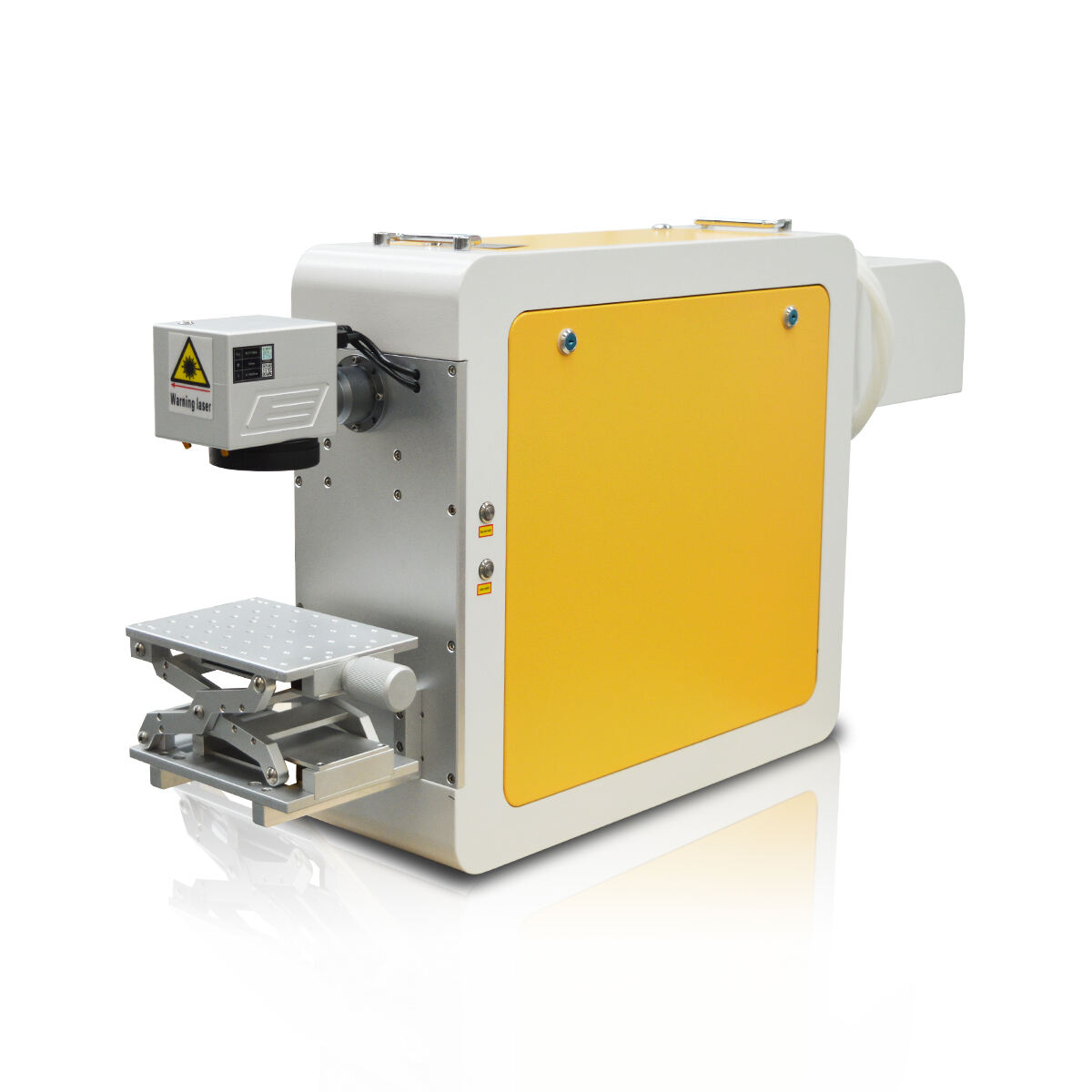